ARTICLE
Going Past Drones as Inspection Tools
GOING PAST DRONES AS INSPECTION TOOLS
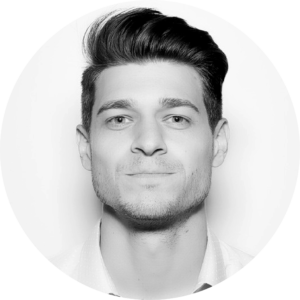
Written by
Josh Meler
Chief Marketing Officer
Generally, low quality drone scans have been useful for inspections only. This is the paradigm Engineering Class 3d data is changing. One Drone scan can serve many different purposes.
One Scan. One Use.
This has been the state of drone data for Telecom for the past 5+ years. Generally, a tower collection is useful for inspections only. While there are a small handful of visual inspection types, traditional drone collections using low quality drones fail to eliminate the need for most truck rolls, or serve to automate structural analysis with any meaningful degree of confidence. This is not because Digital Twin platforms are not smart enough or because AI isn’t mature. Digital Twin tools are throttled by the quality of drone data they analyze.
In recent years, analytics providers have tried extending the use of a single low quality drone collection, but many capabilities are only possible WHEN THERE IS UP-TO-DATE AND ACCURATE LEGACY DATA FOR EACH TOWER. That’s a major asterisk. To account for lack of detail and coverage in a 3d model, Digital Twin companies must reference legacy data to plug in gaps and make an educated guess at measurements or inventory. These companies reference an equipment catalog of thousands of items, and then AI is used to map known dimensions to what is seen in the lower quality drone data to produce tower reports and analysis. In theory this works beautifully. However, in reality, legacy data is rarely trustworthy for complex engineering analysis. Equipment catalogs have hundreds of styles with subtle variations in dimensions (sometimes millimeter differences). For AI to correctly identify equipment, higher fidelity is needed OR existing legacy data needs to be accurate and up-to-date. Again, this is rarely ever the case. So while you could run lower quality drone data through analytics engine to produce engineering reports and analysis, the level of confidence in the automated analysis is very low. Thus, a traditional drone collection is limited to inspection use cases only.
Going Past Inspections
In the next era of industry, drone data must address the big telecom problem – which is not inspections.
Telecom has a legacy data problem, and this in turn drives the need for inspections. Existing databases are incomplete, inaccurate and siloed amongst turf vendors and engineering firms. For drone data to solve for a lack of good legacy data, sensors must collect Engineering-grade 3d tower information (both accuracy and coverage) to effectively reset tower truth. Millimeter attributes like lattice structure width, pipe thickness, bolt sizes and the degree of twist and sway are all essential measurements that technicians must collect. To augment and replace measurements taken in the field, the 3d digital model generated from a drone must achieve no less than this level of detail.

One Scan. Many Uses.
Once drone data can provide Engineering class accuracy and coverage, a single collection can be applied in many ways to provide new value to more stakeholders throughout the tower lifecycle. Critical measurements can automatically be extracted across bolts and brackets. AI can read labels and distinguish between equipment dimensions that differ by millimeters. Standard reports can be generated on-demand. Structural capacity can automatically be extracted, and modifications can be simulated in real-time.
With both millimeter accuracy and 99% surface coverage, an Engineering Class 3D Reality Model establishes a baseline for all future analysis, resetting outdated and incomplete legacy data, and digitizing the site for all future analysis. Digital Twin analysis can then use AI to validate tower inventory, calculate structural capacity, simulate available space, and generate a 3D Design Model.
Moreover, the 3D Reality Model and Digital Twin can be referenced and leveraged repeatably over the tower lifecycle, as future equipment changes and tower modifications are considered. One Engineering Class drone data collection has a considerably longer shelf-life and more applications than traditional Inspection Class collections. Additionally, a single Engineering Class dataset also has utility across enterprise roles.
THE “DRONE DATA GAP” CONTINUUM
Role | Example Uses |
---|---|
Decision Makers | Portfolio direction and decision making |
Engineering | Structure and mount analysis, tower specifications |
Field Operations | Corrective and preventative activities, assessment of tower and compound |
Leasing | Asset identification, ownership and simulation for space selling |
Finance | Commercial verification of assets on structure and ground |
M&A Owners | Infrastructure sell or buy evaluations for M&A activities |
Health & Safety | Environmental issues, climbing assessment, quality installation observations |
Project Management | Inspection planning, remote virtual inspection |
Regulatory | Authority planning, regulatory compliance |
From 1:1 to 1:N
If you’re going to invest in mobilizing a workforce to capture tower data using drones, why not collect a fidelity that’s reusable across the tower lifecycle and serves new use cases that extend beyond inspections? While an Engineering Class tower collection might require marginally more time onsite and involve a more expensive aircraft and sensor, most of the cost to collect tower data is in the mobilization of drone operators themselves. Engineering Class drone data shifts tower collections from a 1:1 model where a single scan provides inspection information only, to a 1:N model where the data can be leveraged across many uses and organizational roles. For drones to graduate from inspection tools, they must solve for poor information data and feed better data into digital twin analytics platforms. Engineering Class drone data is the solution Telecom has been waiting for.