To maintain a living Reality and Design Model over the tower lifecycle, a balanced approach to collection is optimal…
ARTICLE
The False Choice of Inspection Or Engineering Class Drone Data
THE FALSE CHOICE OF INSPECTION & ENGINEERING CLASS DRONE DATA
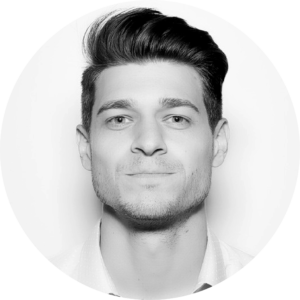
Written by
Josh Meler
Chief Marketing Officer
Towercos have a legacy data problem that gets worse over time, with every subsequent site update. Over their lifecycle, towers undergo a myriad of planned and unplanned changes. Equipment is upgraded. Structures are reinforced. Steel rusts, twists and cracks. What is built is rarely what is designed, and as time passes, legacy data moves farther from the truth.
While inspections do happen, data collection is isolated to a specific part of the tower (ie, second RAD NE side), and collected in a format that is difficult to ingest and rarely accessible across stakeholders. Add to this fact that towers frequently change ownership and are visited by a diversity of third-party vendors, and it’s easy to see how maintaining up-to-date tower data is so difficult.
This is why drones are so interesting. They capture data on the entire tower structure (not just an isolated area), they digitize the site and quantify its attributes (not just photos and a written report), and they do so faster and cheaper than the traditional truck roll (so more data and more often).
Value or volume – the false choice.
But – There are hundreds of variations of drones and sensors, and not every duo is cable of collecting the same quality of 3d data. When collecting tower data, towercos often falsely believe they must choose between highly scalable off-the-shelf drones or more capable enterprise systems – or volume versus value.
On one end of the spectrum, the standard hobbyist-class drone is designed for scale. They are simple to use, affordable, and readily available. However, the sensors on these drones are low-grade, flight time and performance are poor, standoff distance from the tower is dangerous, and issues like EMI interference and GPS drift are more common. Importantly, the class of data these drones produce is constrained to centimeter accuracy, and thus limited to inspection use cases.
On the other hand, professional-class drones are designed to deliver value. While more costly and requiring specialized training, these drones can carry adaptable payloads with improved resolution, better flight performance in challenging conditions, safer flight profiles, and the resulting data offers much better resolution and coverage. This class of drone and sensor is capable of millimeter-accurate Reality Models that can be used to update existing Design Models*, unlocking new forms of automation that apply to Engineering operations also.
This dichotomy creates a false choice for Telecom companies – “Do I need an Inspection or Engineering class drone data collection?”
About Reality and Design models
When choosing the “right” drone and sensor for the job, it is really a question of the resulting Reality Model and Design Model requirements, as well as the existing tower datasets.
3D data collected from drone sensors serves as the basis for Digital Twin analysis. Drone sensors (cameras) blanket a tower structure with thousands of 2D photos to triangulate a 3D point cloud, and then generate a 3D Reality Model. If the resulting model offers engineering-grade accuracy, the 3D model can then be used to generate a new structural Design Model that is analyzed by AI/ML engines to extract structural limits or estimate capacity. Thus, the more accurate the 3d model, the greater the confidence in automated analysis.
This brings us back to the choice – Should I invest in the more expensive class data collection that can produce an up-to-date Design Model, or will a lower quality inspection-class 3d model suffice?
This creates a difficult choice. Fortunately, it’s not an either-or proposition.
An integrated approach
To maintain a living Reality and Design Model over the tower lifecycle, a balanced approach to collection is optimal. This means integrating both Inspection and Engineering Class drone systems, depending on the physical tower change that has occurred. As a general rule, Engineering Class Reality Models refreshes (drone collections) are only needed when there has been a structural change, such as when additional equipment and steelwork has been added. For other changes, such as equipment changes or condition analysis, a Standard Inspection Class drone inspection is sufficient. In the figure below, we’ve outlined a series of events that commonly occur over the tower lifecycle, with the prerequisite drone collection class.
It is important to first collect an Engineering Class baseline Reality Model to reset legacy data and generate an up-to-date Design Model. Only after this is collected can Standard Inspection Class datasets be used to estimate and make inferences. A Standard Class Reality Model alone cannot gauge metal thickness, detect subtle differences in equipment make and model – and is not capable of producing a Design Model with any acceptable level of confidence.
Conclusion
As 5G rollouts begin, there is a widening gap between physical reality and legacy information. And while drone technology promises to refresh site data, many companies often falsely believe that they must choose between data from hobbyist class drones that provide scale and professional class drone platforms that deliver more valuable data. Fortunately, it’s not an either-or decision. To maintain a living Reality Model and up-to-date Design Model, tower companies must adopt an integrated approach to both Engineering and Inspection Class drone data collections over the tower lifecycle.
*Patented Visual Intelligence dual-sensor technology is capable of collecting sub-millimeter accuracy across 99% of a structures surface.